Case Study: Fire Department responds to high levels of Hydrogen Cyanide post residential air conditioning installation.
Mike Bloski
Introduction
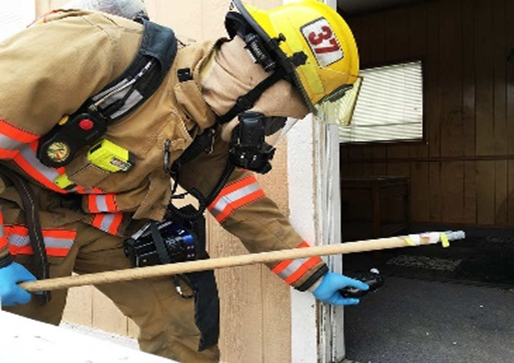
Recently, our hazardous material response team was asked to provide mutual aid to another department related to a carbon monoxide fire alarm activation after a commercial company was replacing or installing a new air conditioner unit. The location was a typical Florida high-rise unit with several units and the occupant was replacing their unit that was installed in 1997. Upon the fire department’s arrival, they deployed their air monitoring detection to check the unit for hazards. They found elevated levels of both carbon monoxide (CO) and hydrogen cyanide (HCN) on two detector units being used. The CO level was 5–10 ppm and the HCN levels were topped at 49.5 ppm. These readings were taken 25-minutes post alarm and after the installation by a local air conditioning company that conducted soldering operations on an entire new AC unit. They began an aggressive ventilation plan and rechecked after 15–20 minutes. They returned for a recheck and found that elevated readings of CO and HCN remained. In addition, adjoining units were checked, and no atmospheric hazards found. They contacted our district to respond and verify the readings as correct. Upon our dispatch, I spoke with the on-scene Incident Commander (IC) and asked him to stop ventilation and close the unit to recreate or trace the elevated units with our photoionization detector (PID) upon our arrival. Upon our arrival on scene, the IC stated that upon closing the door to reseal the unit, the levels of CO and HCN had dropped but were still present. We made an entry 1.5 hours after the alarm and walked through, finding CO at 1.5 ppm and HCN at 3 ppm. An interview was conducted with the on-scene representative with the air conditioning, and they stated that their work was conducted by company policy to install the unit, confirming they had conducted soldering work in the unit. There were no health-related problems from the occupant or workers. The question was what caused the high readings? Research from common sources conducted on scene and former responses stated the by-products of the soldering operations caused the elevated CO and HCN readings but why? During the research phase, I ran across an article in Fire Engineering Training Community blog by Timothy Gaffney. He noted that he ran a similar incident where there were elevated readings and after investigation, it was found a water heater was installed using soldering for the pipes but unsure why his crew found the elevated readings ruling out common sources (Gaffney, 2011). The purpose of this article is to give a better explanation of why these elevated readings are encountered.
Soldering or Fluxing (which is it?)
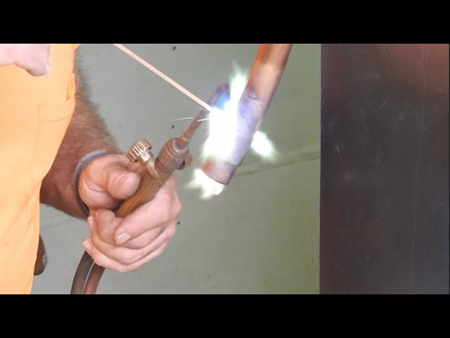
Soldering is the act of joining two metals together; flux is the bond that brings the two metals together to ensure clean, crack-free adhesion. When joining metals, an acid is typically used to remove oxidation; it makes the solder “wetter,” causing better flow over surfaces. There are several types of flux based upon the metals that are being joined (Chemtronics, 2024). The composition of flux wiring is determined by the metals fused together. Fluxes for soft soldering are typically organic in nature, usually based on halogenides or acids. When soldering using flux, the user produces a high amount of temperature; therefore, the production of heavy vapors and medal oxidizing formation takes place (Humpston & Jacobsen, 2002). There is no acute health hazards associated with soldering, as long as the space is well ventilated. When heated during soldering operations, these products may generate irritating and toxic fumes of lead oxide, tin oxides, hydrogen chloride, zinc oxides, and ammonium compounds. Hydrogen Chloride (HCl) may be the link to why our detectors behave the way they do.
By-Product Examination
Knowing that one of the byproducts of soldering is the production of HCl we can dive into how the interaction works with detectors. HCl is a colorless gas at room temperature that can be found as a large component of soldering materials. This is a large part of the acid fluxes. The danger of chronic exposure can be explained with this ATSDR document, that explains that this non-flammable gas is used in industry for electro plating metals, when off-gassed by soldering and coming in contact with water vapor (humidity), we get the formation of hydrochloric acid (Agency for Toxic Substances and Disease Registry, 2002). This is why some industry workers report a metallic taste in the mouth after soldering or brazing.
Our Response to Incidents
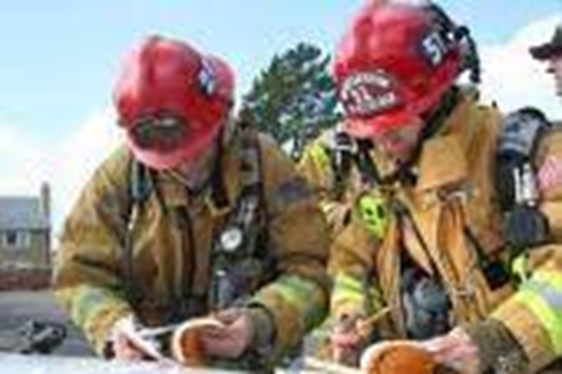
As we examine our response, it is typical to bring in a fire service 4-gas detector to examine the atmosphere in volume for hazards. Typically, the fire service brings a 4-gas detector that has a HCN sensor as we examine the atmosphere in post-fire extinguishment inside an enclosed structure. The myth common in the fire service is to prove it is not there and it is safe to remove your SCBA. This is false, as we have to understand the long-term exposure to HCN and maintain vigilance while wearing our SCBA at all times in post-fire situations. As stated, we dive into the HCN sensor and understand it is one of our most temperamental sensors in existence. Most manufacturer-installed HCN sensors have a range of 1–50 ppm. They work via an electronic cell sensor with an accuracy of +/- 5%. However, we should understand that typical response times of these sensors is greater than 30 seconds. Understanding the chemistry of HCN, we should note that it remains a liquid at <78 F degrees and then converts to vapor at greater temperatures. It has a vapor pressure of 630 mm Hg to explain the temperature conversion (Department of Health and Human Services, 2010). HCN is widely used in a variety of applications, including fumigation and metal plating. It is manufactured from the combination of ammonia and natural gas and is a precursor to many chemical compounds. It is noted as an effective chemical warfare agent.
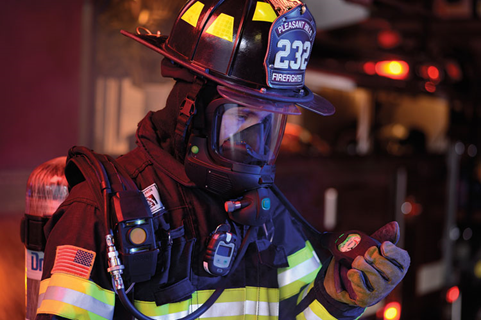
With its low exposure, HCN is immediately dangerous to life and health (IDLH) at 50 ppm. In addition, it is worthy to note that HCN is a Class IA Flammable liquid with lower explosive limit at 56,000 p.m., or 5.6% by volume. It is also considered at times anhydrous in nature and would seek water or humidity in associated signs and symptoms to patients. HCN exposure of the last decade has been identified as a significant chemical in post-structural air monitoring as many of the modern components of home construction (e.g., polyurethane foams used in furniture) can release large amounts (Blackline Safety, 2024). The toxicity to humans’ results from metal-containing enzymes being blocked by HCN to prevent oxygen for cell respiration. Over toxicity is usually fatal. One of the major hazmat concerns with the sensor is cross-sensitivity, the main component being Hydrogen gas-related (RAE HCN sensors are x 200 to true readings). This would explain the attraction to HCl as a by-product of soldering operations and why abnormal HCN sensor levels occurred. Why the high CO readings? This can be associated with the heat source (brazing gas) used in the soldering operations, which was confirmed with the company on site.
Conclusion Our responses to unknown atmospheres are challenging in the fire service. Understanding the reason requires some detective work and past experiences. In addition, awareness that built in sensors in -4-gas detectors are well designed but are known to have cross-sensitivity issues that must be accounted for. Elevated levels of CO and HCN were detected due to soldering during air conditioning unit replacement, emphasizing the importance of proper ventilation and air monitoring by the installing company. By recognizing the by-products of soldering and their potential health risks, we can better prepare and respond to similar situations, ensuring the safety of both first responders and occupants.
Works Cited
- Agency for Toxic Substances and Disease Registry. (2002, April 1). Hydrogen Chloride. Retrieved from ATSDR: https://www.atsdr.cdc.gov/toxfaqs/tfacts173.pdf
- Blackline Safety. (2024, January 1). Intro to Hydrogen Cyanide Gas. Retrieved from Blackline Safety: https://www.blacklinesafety.com/solutions/gas-sensors/hcn
- Chemtronics. (2024, January 1). Choosing the best flux for high qualitiy electronic soldering. Retrieved from Chemtronics: https://www.chemtronics.com/essential-guide-to-flux-for-soldering-electronics#:~:text=Flux%20plays%20a%20crucial%20role,molten%20alloy%20known%20as%20solder
- Department of Health and Human Services. (2010). NIOSH pocket guide to chemical hazards No. 2010-168c. Neenah: J.J Keller & Associates.
- Gaffney, T. (2011, March 11). CO turn cyanide turn false? Retrieved from Fire Engineering Training Community blog: https://community.fireengineering.com/m/blogpost?id=1219672%3ABlogPost%3A286489
- Humpston, G., & Jacobsen, D. M. (2002). Princples of soldering. Detroit: AMS International