One Simple Thing
Kevin Ryan
Hazmat incidents can often become complex and over-complicated. It is not uncommon to see paralysis by analysis taking place. Simple and efficient Incident Management principles can often get bypassed, overlooked, or ignored.
One of the most basic yet essential principles is that of control zones. Establishing the hot, warm, and cold zones are your ticket to success at an incident. The reality of this principle really became obvious to me during recent department wide training in the Baltimore City FD (BCFD). The BCFD conducts weekly 2 and 1 training that covers various topics relevant to all members of the department. Hazmat had the privilege of presenting a natural gas leak response during the last (8) months. We are no different than most departments in that we suffer from complacency when faced with these responses.
In the year 2022, there were over 1100 recorded responses for leaking natural gas in Baltimore. The interactions with the members who take these responses every day proved to be valuable in our assessment of how to improve. Complacency was leading to the ignorance of adhering to basic hazmat response principles. Lack of control zones, exposing to many personnel, poor apparatus placement, meter training are just some of the issues identified.
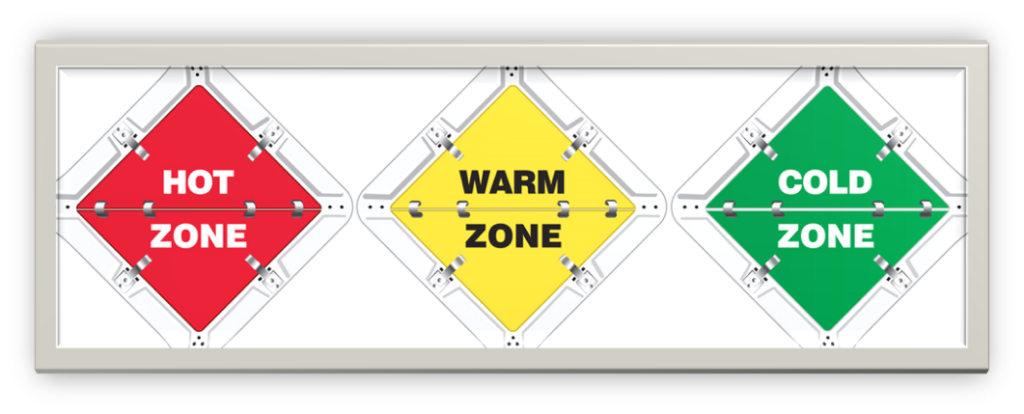
One simple thing stood out to me throughout the entire training cycle. The one thing that most of us took for granted is the key to a successful incident. What could be so simple that brought so much success? The establishment of a hot zone was one common factor in every single successful hazmat incident I have ever been witness to. Could it really be that easy to ensure a successful outcome despite the ever-changing scenarios that we face? Why was this possible? What does a hot zone do for our incident? The answer lies in the fact that it establishes a clear playing field that all members understand. It means ICS established, full PPE, minimal entry, RIT teams, decon etc. The simple act of establishing a hot zone frames the incident for everyone involved. Framing the incident in this manner provides a clear picture to the members involved. Incident Commanders (IC’s) now have 3-dimensional areas to assist with accountability and removing free lancing from the equation.
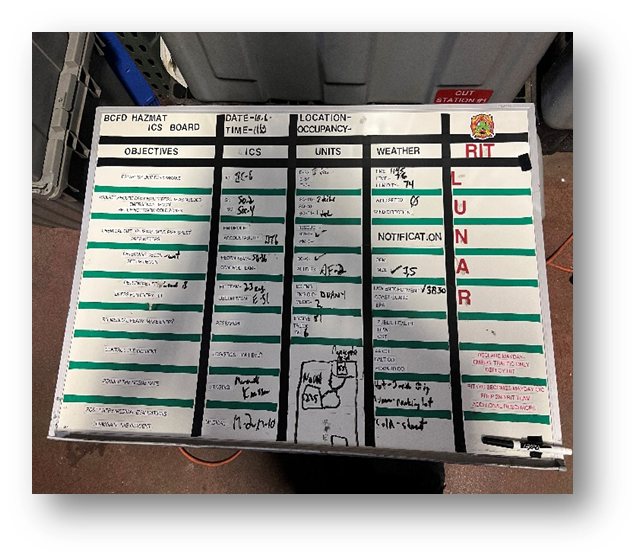
Incident Command Systems (ICS) exist on 2-dimensional command boards and via radio traffic. The hot, warm, and cold zones can be visually defined so that members know where they are supposed to be operating. A clear briefing from the IC will denote these three separate zones.
An example of this was a mixed chemical reaction incident at a local cola bottling plant in East Baltimore. The reaction took place in a mechanical room where sodium hydroxide was stored and came in contact with a peracetic acid sanitizing solution. A small hallway from the mechanical room led to the open warehouse floor with a doorway to the main office area nearby. The IC of the incident informed all members by announcing the control zones at the beginning of the briefing.
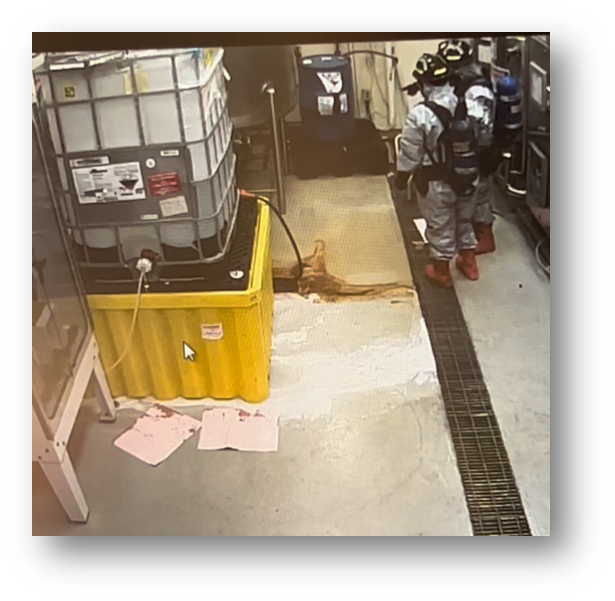
The hot zone was designated as the area around the small hallway, warehouse and office area. The office area was access controlled, so accountability was easy to manage for the Safety Officer. The warm zone was set up just beyond the access point with decon at the ready. The cold zone was set at the street where the Incident Command Post (ICP) had a clear view of the building and members entering\exiting the hot zone. The simple act of establishing a hot zone defined the incident for all members. It is no surprise that this incident ended successfully because of our Hazmatters understanding their roles. The physically defined areas enhanced that understanding. The beauty of this is in its simplicity. The control zones are basic actions that can be taken by initial responders arriving on scene first. Your first arriving IC does not even have to be a hazmat tech to implement these principles. A strong approach to the basics will reap success at every incident encountered. All it takes is One Simple Thing to put you on the path to success. problem.